Selecting the Right Ball Valve for High-Temperature Applications
Ball valves for high temperature applications need to handle at least 200°C without failing. Look for stainless steel construction (grades 316, 321, or 347), metal seats for extreme heat, and temperature ratings that exceed your maximum operating temperature by 50°C. These features prevent the seal failures and material breakdown that destroy standard valves in high-heat environments.
The right valve choice saves you from expensive emergency repairs and keeps your operations running safely when temperatures reach 500°C (932°F) or higher.
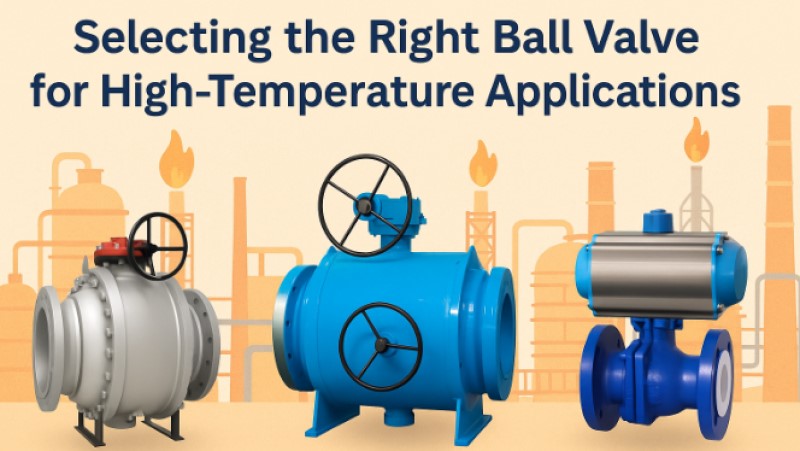
Why High-Temperature Applications Destroy Standard Valves
High temperature ball valve applications are tough on equipment. When fluids get above 200°C (392°F), regular valve materials start breaking down, seals melt or crack, and thermal expansion causes parts to bind up or leak.
Power plants, refineries, and chemical processing facilities regularly run at temperatures that would wreck standard valves in weeks. High temp ball valve designs handle these conditions by using better materials and accounting for how metal expands and contracts with heat.
What to Look For in High-Temperature Ball Valves
When selecting high-temperature ball valves, focus on these key factors to get the most value from your purchase:
Temperature Ratings
Your valve needs to handle more heat than your system produces. High temperature valve specs should show at least 50°C (90°F) above your maximum operating temperature. This safety margin accounts for unexpected temperature spikes that happen in real-world operations.
Most industrial ball valves for high temperature work handle 200°C to 500°C (392°F to 932°F) continuously. For really extreme jobs, specialized valves can go up to 650°C (1200°F), but these need custom engineering.
Material Construction
Another factor that determines the performance of high-temperature ball valves is material. These valves come in a variety of forms, with each offering a specific benefit to the user:
Material Comparison for High-Temperature Ball Valves:
Material Grade | Max Temperature | Key Benefits | Typical Applications |
---|---|---|---|
316 Stainless Steel | 400°C (752°F) | Corrosion resistance | Chemical processing |
321 Stainless Steel | 450°C (842°F) | Stabilized for welding | Power generation |
347 Stainless Steel | 500°C (932°F) | Superior creep resistance | Oil refining |
Hastelloy C-276 | 650°C (1200°F) | Extreme corrosion resistance | Specialized chemicals |
Carbon steel stops working above 400°C because it oxidizes and loses strength. Stainless steel grades 316, 321, and 347 are your best options for high temperature ball valve applications; each one works better in different situations.
Seats Design
Seat material makes or breaks valve performance in high heat. Freeze proof ball valve applications need seat materials that stay flexible through big temperature swings, especially when equipment cycles between hot operation and cold shutdowns.
Seat design for different temperatures:
- 200-250°C: Reinforced PTFE with carbon or glass fiber
- 250-400°C: PEEK or metal-backed PTFE
- 400°C+: Metal seats (stainless steel or stellite-faced)
Valve Design That Handles Heat
Three-piece ball valve designs work best for high-temperature jobs because they can expand without jamming. The separate body pieces move independently when heated, so the valve doesn’t bind up.
Two-piece designs are okay for moderate high-temperature work but might stick during heating and cooling cycles. One-piece designs should be avoided in high-temperature applications because they can’t handle the thermal stress.
Where High-Temperature Ball Valves Get Used
Different industries have different high-temperature challenges, but they all need valves that won’t quit when things get hot. Here’s where these specialized valves prove their worth:
Power Plants
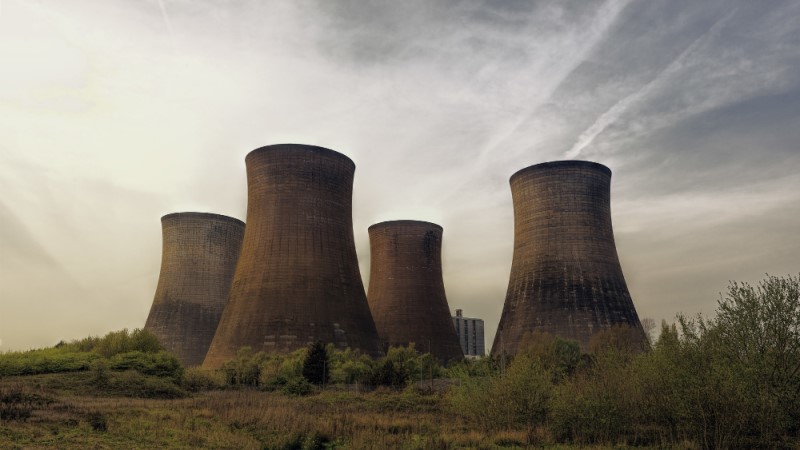
Steam systems run up to 540°C (1000°F) at crazy high pressures. High temperature valve choices need to handle superheated steam and still shut off completely during emergencies.
Refineries
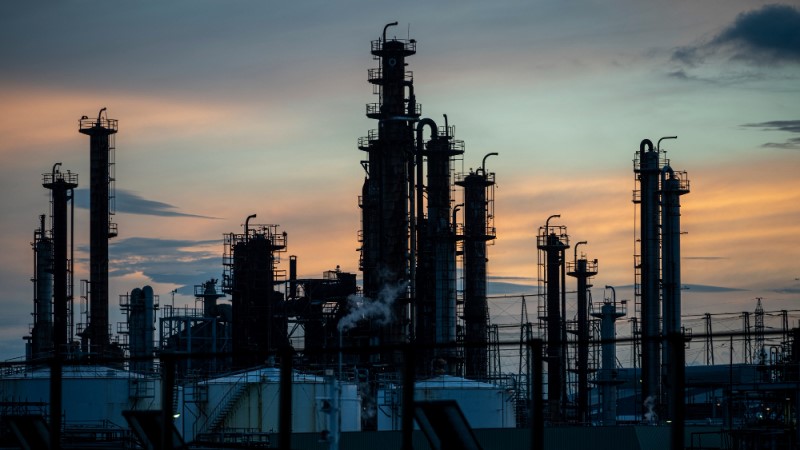
Hot oil, acids, and other nasty chemicals eat through regular valves. Ball valves for high temperature refinery work need special coatings and corrosion-resistant materials to last.
Oil and Gas
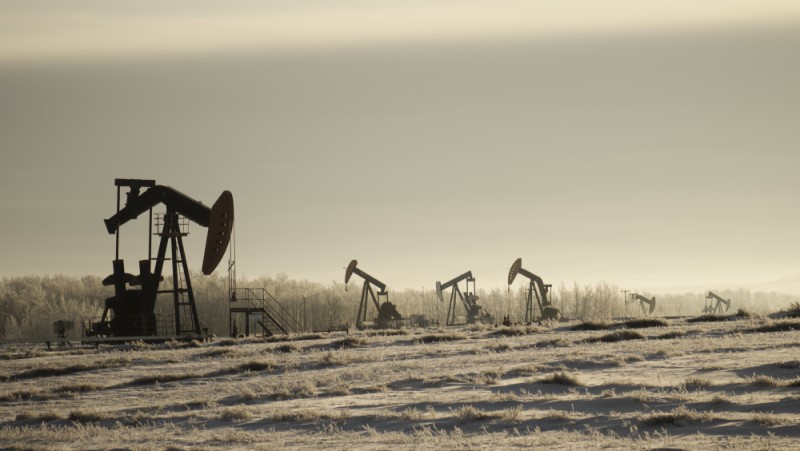
Wellheads and processing equipment see temperatures up to 400°C. Freeze resistant ball valve designs are essential where temperatures swing from -40°C to 400°C depending on season and operating conditions.
PANS Valve High-Temperature Solutions
The high temperature resistant materials and design of PANS valves incorporate decades of engineering experience in extreme service applications. Our high temperature ball valve designs feature:
Advanced material technologies:
- Premium stainless steel alloys tested for high-temperature service
- Specialized seat materials engineered for thermal cycling
- Anti-galling stem coatings for reliable operation
- Fire-safe designs meeting API 607 standards
Proven design features:
- Extended bonnets to protect packing from extreme heat
- Blow-out proof stem design for safety
- Metal-seated options for ultimate temperature resistance
- Freeze proof ball valve configurations for extreme climate applications
Our manufacturing process includes high-temperature testing to verify performance under actual operating conditions, ensuring reliable service in your critical applications.
Standards and Certifications
Beyond just surviving high temperatures, your valves need to meet industry standards that prove they’re safe and reliable. These certifications are your insurance that the valve will work when you need it.
Important standards include:
- API 6D: Pipeline valve specs for pressure and temperature
- API 607: Fire-safe testing for emergency situations
- ASME B16.34: Valve design standards for pressure-temperature ratings
- ISO 15848: Emissions testing for environmental compliance
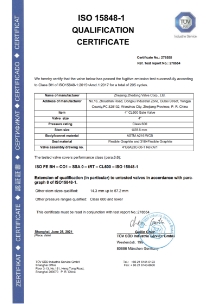
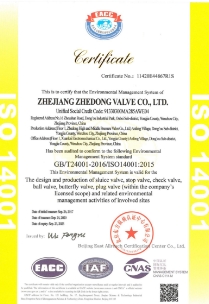
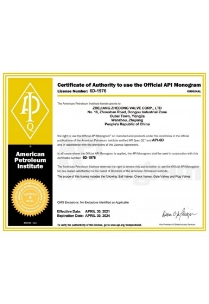
These standards make sure valves work safely in high-temperature applications while meeting environmental and safety rules.
Installation and Maintenance Tips
Proper installation matters for high temperature valve performance. Leave room for thermal expansion, use gaskets rated for your operating temperature, and make sure piping supports can handle thermal growth.
You’ll also want to:
- Inspect during scheduled shutdowns
- Watch packing performance and adjust when needed
- Look for thermal stress or corrosion signs
- Keep spare parts on hand for critical applications
Freeze resistant ball valve installations need insulation and heat tracing to prevent freezing during shutdowns.
Getting the Right Valve for Your Job
Choosing the right ball valves for high temperature work means balancing performance with cost. Premium materials and specialized designs cost more upfront, but they last longer and cause fewer problems in tough applications.
PANS Valve’s comprehensive ball valve collection includes high-temperature solutions built for the most demanding industrial jobs. Our team can help specify the right valve setup for your specific temperature and service needs.
Contact PANS Valve today to discuss your high-temperature valve requirements and get reliable performance in your critical applications.
Search
Categories
Tags
Product
- Ball Valve
- Floating Ball Valve
- Fully Welded Ball Valve
- Trunnion Ball Valve
- Check Valve
- Cast Lift Check Valve
- Cast Swing Check Valve
- Wafer Type Check Valve
- DIN Valve
- DIN Bellow Sealed Globe Valve
- DIN Globe Valve
- DIN Rising Stem Gate Valve
- DIN Swing Check Valve
- Forge Valve
- Forged Check Valve
- Forged Floating Ball Valve
- Forged Gate Valve
- Forged Globe Valve
- Gate Valve
- Bellow Sealed Gate Valve
- Flat Gate Valve
- Wedge Gate Valve
- Globe Valve
- Cast Globe Valve
- Plug Valve
- Eccentricity Plug Valve
- Inverted Pressure Balance Lubricated Plug Valve
- Orbit Plug Valve
- Sleeve Type Plug Valve
- Slurry Valve
- Slurry Valve
- Strainer