How to Choose the Right Plug Valve for Oil & Gas Projects
Choosing the right plug valve requires considering your media type, pressure and temperature conditions, shut-off requirements, and how often the valve will be maintained.
If you’re dealing with clean gas, you might prefer a non-lubricated option. If you’re handling crude oil or abrasive flow, a pressure-balanced lubricated design is often the better choice. And if your application needs a tight shutoff or automation, orbit plug valves make more sense.
Below, we break down the key factors that influence selection so you can match the right valve type to your specific oil or gas application.
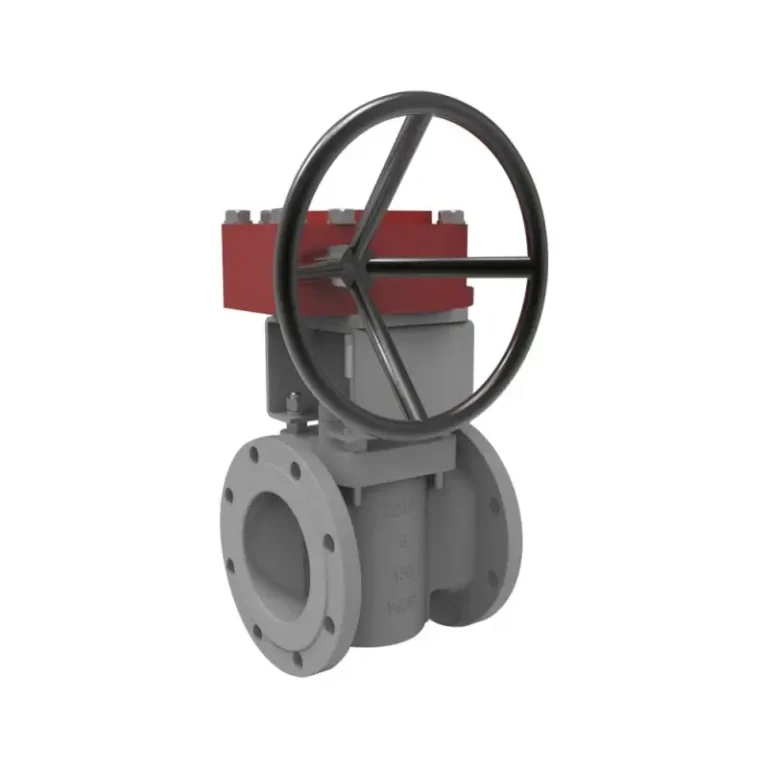
Why do so many projects choose our Plug Valves?
From sealing performance to durability, we deliver professional-grade solutions.
What Makes Plug Valves Ideal for Oil & Gas Systems
Oil plug valves and gas plug valves play a critical role in upstream, midstream, and downstream operations. Their quarter-turn design allows fast actuation, tight sealing, and easy inline service. More importantly, plug valves are built to handle media that may be viscous, high-pressure, or corrosive.
In the oil and gas industry, plug-type valves are often installed in pipelines carrying fuel oil, crude, natural gas, LPG, and various petrochemical products. Their straight-through flow path allows minimal turbulence, and the robust sealing system makes them ideal for shutoff, isolation, or bypass functions in critical systems.
Plug Valve Types and When to Use Them
Each valve has strengths based on how it’s constructed and what kind of operation it supports. Here’s how to determine which plug valve fits your specific oil or gas project:
Sleeve Type Plug Valve
This non-lubricated valve uses a PTFE or elastomeric sleeve to reduce friction and prevent leakage. The plug rotates inside the sleeve, creating a tight seal without metal-to-metal contact.
You can use it in clean gas service, refined fuel lines, or corrosive applications where long-term lubrication isn’t ideal. Since the design is self-sealing and low-maintenance, it’s preferred in gas pipelines and chemical injection systems.
Our sleeve plug valves are tested to API 599 and API 6D standards and are compatible with both manual and automated operation.
Inverted Pressure Balance Lubricated Plug Valve
If you’re dealing with high-viscosity or abrasive media such as unrefined crude, slurries, or high-temperature flow, this is your best option. The body includes grooves for injecting sealant between the plug and the valve body, which helps maintain sealing integrity under pressure.
These oil plug valves are built to withstand thermal cycles, system pressure surges, and media with suspended particles. They’re widely used in upstream production units, tank farms, and heavy oil pipelines.
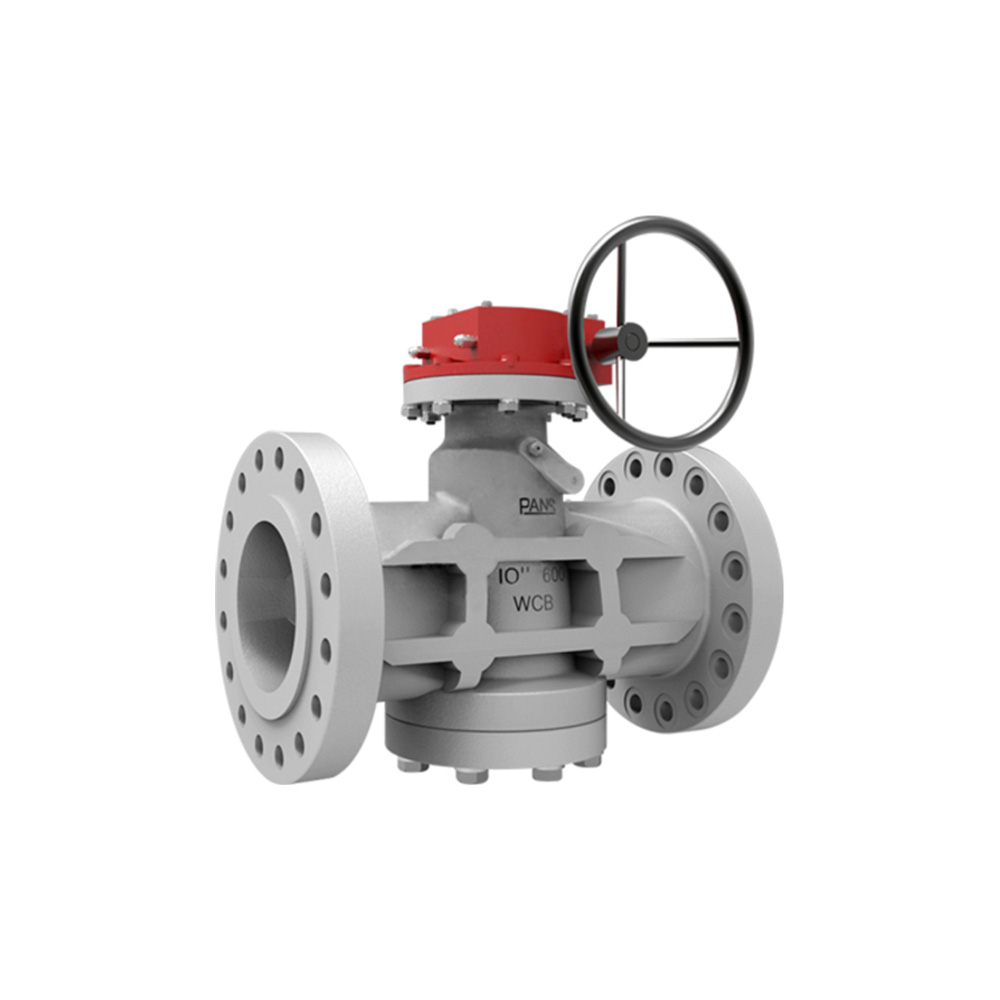
Inverted Pressure Balance Lubricated Plug Valve | PANS
More DetailsOrbit Plug Valve
If your project requires zero leakage, frequent cycling, or automation, orbit plug valves provide dependable shutoff with minimal wear. The design eliminates sliding friction during open/close, which improves longevity and makes them suitable for critical gas service, separators, or metering stations.
They can be configured for electric, pneumatic, or manual operation, and are compatible with remote actuation in automated systems.
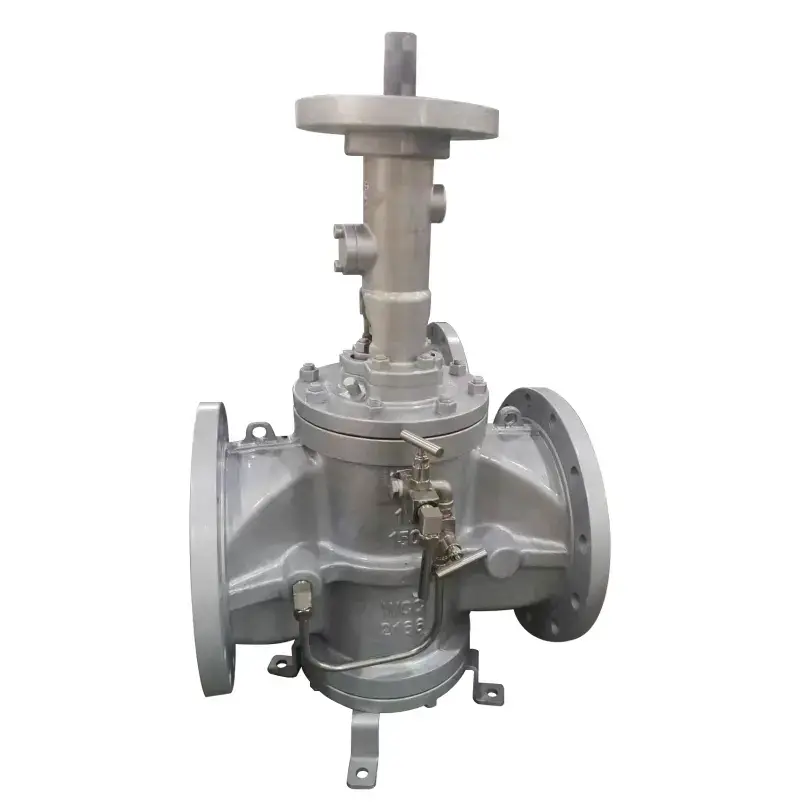
Orbit Plug Valve | PANS
More DetailsKey Factors That Influence Your Selection
The best plug valve depends on your operating environment and service conditions. Here’s what to evaluate before selecting:
Media Type
What’s flowing through the pipeline? Clean gas, refined fuel, slurry, or corrosive media like sour gas each require different sealing methods and materials. For example, abrasive fluids wear down unprotected metal surfaces faster, so a lubricated or lined design works better.
Pressure and Temperature
Systems operating under high pressure or exposed to thermal cycling need valves with pressure-balancing features. Lubricated plug valves use injected sealants to maintain a tight seal across fluctuating loads and temperatures. Orbit designs can also handle frequent actuation without degradation under thermal stress.
Maintenance Frequency
In remote facilities or high-risk zones, maintenance access is limited. A sleeve-type plug valve helps minimize service needs thanks to its low-friction seal and long wear cycle. Lubricated valves perform better under stress but require periodic sealant injection to maintain performance.
Shut-Off Requirement
Some pipelines cannot afford leaks. If you’re managing safety-critical lines like gas metering, bypass loops, or ESD applications, orbit plug valves offer a torque-seated shutoff that ensures zero leakage and reliable resealing after every cycle.
Automation and Actuation
Manual valves are sufficient for low-cycle use. But when automation is required—for example, in compressor stations or separator skids—look for plug valves compatible with electric or pneumatic actuators. Orbit plug valves excel in these conditions due to their low operating torque and wear-free sealing.
Certifications That Ensure Global Compliance
All oil and gas valves are manufactured under the following systems and standards:
- ISO 9001, 14001, and 45001 quality management
- CE, TUV, and PED certification for international exports
- Full compliance with API 6D, API 599, and ASME B16.34
These certifications ensure every product meets the requirements for valves in the oil gas market, from EPC contractors to end users in refineries and distribution facilities.
Matching Valve Types to Common Oil & Gas Applications
Different stages of oil and gas projects demand different valve functions. Some lines need tight shutoff. Others prioritize corrosion resistance or low maintenance. Below is a simplified guide to help match plug valve types to service conditions:
Application | Media Type | Pressure | Recommended Valve |
---|---|---|---|
Gathering lines, gas fields | Dry or sour gas | Low to medium | Sleeve Plug Valve |
Crude oil transport, separator lines | Viscous or dirty oil | Medium to high | Inverted Pressure Balance Lubricated Plug Valve |
Offshore platform shutoff | Mixed-phase flow | High | Orbit Plug Valve |
Fuel oil terminals | Refined fuel, jet fuel | Medium | Sleeve Plug Valve |
Refinery isolation lines | High-temp hydrocarbons | High | Lubricated Plug Valve |
All valve types listed here are widely used in oil and gas systems, from gathering lines to metering skids. They are designed for high-cycle use, meet API and ASME standards, and can be configured for manual or automated control.
Why Buyers Prefer PANS for Plug Type Valves
As a plug valve manufacturer with over 36 years of experience, we help keep operations safe, efficient, and compliant. With more than 100 international patents, exports to over 60 countries, and in-house machining and testing, our products support large-scale energy, petrochemical, and industrial projects.
From oil gas valves to check valves, gate valves, strainers, and complete pipe system kits, we support one-stop procurement for contractors and OEMs worldwide.
Request a Custom Quote Today
If you’re looking for a certified gas valve manufacturer or need quick delivery on oil plug valves, contact our team. We’ll help you select the right plug type valve for your service conditions—on time and on spec. Start sourcing industrial valves backed by engineering, reliability, and fast global delivery.
Search
Categories
Tags
Product
- Ball Valve
- Floating Ball Valve
- Fully Welded Ball Valve
- Trunnion Ball Valve
- Check Valve
- Cast Lift Check Valve
- Cast Swing Check Valve
- Wafer Type Check Valve
- DIN Valve
- DIN Bellow Sealed Globe Valve
- DIN Globe Valve
- DIN Rising Stem Gate Valve
- DIN Swing Check Valve
- Forge Valve
- Forged Check Valve
- Forged Floating Ball Valve
- Forged Gate Valve
- Forged Globe Valve
- Gate Valve
- Bellow Sealed Gate Valve
- Flat Gate Valve
- Wedge Gate Valve
- Globe Valve
- Cast Globe Valve
- Plug Valve
- Eccentricity Plug Valve
- Inverted Pressure Balance Lubricated Plug Valve
- Orbit Plug Valve
- Sleeve Type Plug Valve
- Slurry Valve
- Slurry Valve
- Strainer