Selecting Forged Valves for High-Pressure Applications
Choosing forged valves for high-pressure applications requires considering pressure ratings that exceed operating conditions, material compatibility with process fluids, and temperature resistance for your specific environment.
You also need to evaluate flow characteristics, safety margins, end connection requirements, and compliance with industry standards.
Additional factors include high pressure valve for water systems, specialized designs for marine applications how ball valves adapted, and comprehensive testing protocols that verify performance under extreme conditions.
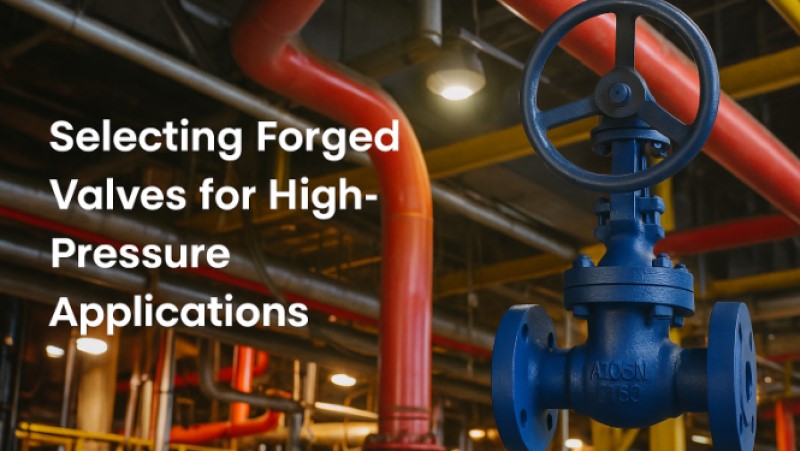
Why High-Pressure Applications Need Special Valves
High-pressure systems operate where standard valves fail. Steam systems, chemical processing, and marine operations create conditions that destroy regular valve designs through extreme pressures, temperature cycling, and corrosive environments.
When pressures exceed 1,500 PSI and temperatures reach 1,000°F, valve failure means more than just replacement costs. You’re looking at safety risks, environmental damage, and expensive plant shutdowns.
Why Forged Steel Works Better for Extreme Conditions
The right material makes the difference between reliable service and catastrophic failure. Forged steel eliminates the weak spots found in cast valves. The forging process creates uniform, dense material that handles pressure stress without cracking or deformation.
Key advantages:
- Higher strength for pressure resistance
- Better fatigue resistance under cycling loads
- Eliminates internal voids or weak spots
- Superior impact resistance
Understanding Pressure Ratings
Pressure ratings aren’t just numbers – they’re safety guidelines that prevent failures. Every valve has maximum pressure limits at specific temperatures.
Common High-Pressure Classes
- Class 600 – Moderate high-pressure service
- Class 900 – Standard industrial high-pressure
- Class 1500 – Heavy-duty extreme pressure
- Class 2500 – Specialized critical applications
Safety Margins Matter
Always select valves rated at least 25% above your maximum operating pressure. This accounts for pressure surges and provides safety margins for unexpected conditions.
Temperature Derating Considerations
Pressure ratings decrease as temperature increases. Always verify pressure-temperature curves for your specific operating conditions to ensure safe operation throughout the expected temperature range.
Matching Materials to Applications
Application | Material | Pressure Range | Why It Works |
---|---|---|---|
Steam Systems | 316 Stainless Steel | Up to 2,500 PSI | Heat resistance + strength |
Water Service | Carbon Steel/316 SS | Up to 1,500 PSI | Corrosion resistance |
Marine Use | 316L Stainless Steel | Up to 1,200 PSI | Saltwater resistance |
Chemical Processing | 347 Stainless Steel | Up to 2,000 PSI | Chemical compatibility |
High-Pressure Valve Types
Different valve types excel in specific high-pressure applications. Choose based on your flow control needs and operating conditions.
Globe Valves for Precise Control
Forged steel globe valve high pressure & temperature applications need the precise throttling that globe valves provide. They handle extreme conditions while giving accurate flow control.
Globe valves excel in steam bypass systems, boiler feedwater control, chemical processing, and power plant operations where precise flow regulation is essential.
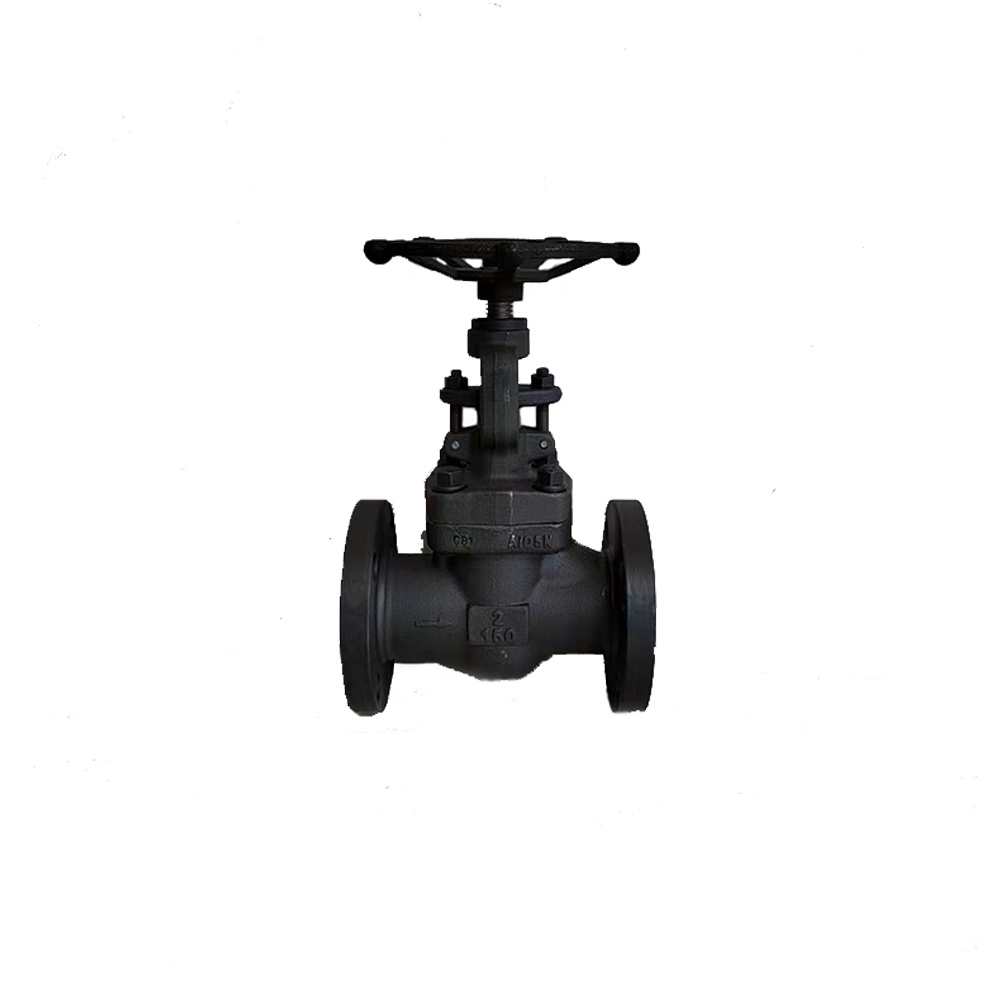
Forged Globe Valve | PANS
More DetailsBall Valves for Quick Operation
Ball valves excel in on/off service where fast operation matters. For marine applications how ball valves adapted includes specialized materials and fire-safe designs for offshore safety.
Marine adaptations include enhanced saltwater corrosion resistance, fire-safe certification for offshore use, quick emergency operation capability, and robust mounting systems designed for harsh marine conditions.
Gate Valves for Full Flow
Gate valves provide unobstructed flow when fully open, ideal for applications needing minimal pressure drop.
Application-Specific Design Requirements
Different industries present unique challenges requiring specialized valve features and design considerations.
Water System Applications
High pressure valve for water applications face unique challenges including water hammer, corrosion, and temperature variations from near-freezing to superheated conditions.
Water-specific design features include:
- Pressure surge protection through controlled operation
- Corrosion-resistant materials and coatings
- NSF certification for potable water applications
- Drain connections for freeze protection
Marine Environment Considerations
Marine applications create extreme conditions requiring specialized valve engineering. Salt spray, temperature extremes, and safety requirements demand robust solutions.
For marine applications how ball valves adapted includes 316L stainless steel for superior corrosion resistance, fire-safe certification meeting IMO standards, position indicators for remote monitoring, and locking mechanisms preventing unauthorized operation.
Chemical Processing Requirements
Chemical processing environments expose valves to corrosive fluids, extreme temperatures, and toxic materials. Valve selection must consider chemical compatibility, fugitive emissions requirements, and emergency shutdown capabilities.
Selection Criteria
When selecting forged valves for high-pressure applications, ensure you’ve evaluated maximum working pressure including surge conditions, operating temperature range and thermal cycling, flow requirements and pressure drop limitations, and fluid compatibility with corrosion considerations.
Also consider valve type for your specific application, end connections and installation requirements, actuation needs whether manual or automated, and required safety features for emergency operation.
Finally, verify compliance with industry standards like API, ASME, and ANSI, certification requirements for your industry, testing documentation needs, and available maintenance and service support.
Installation and Maintenance
Proper installation and maintenance ensure long-term reliable performance in high-pressure applications.
Proper installation requires adequate support to prevent piping stress, alignment verification to prevent binding, appropriate gaskets for pressure and temperature conditions, and following specified torque requirements for proper sealing.
Regular maintenance includes inspection for wear or damage, periodic pressure testing to verify integrity, scheduled lubrication of moving parts, and maintaining spare parts inventory for critical service applications.
PANS Valve Engineering Excellence
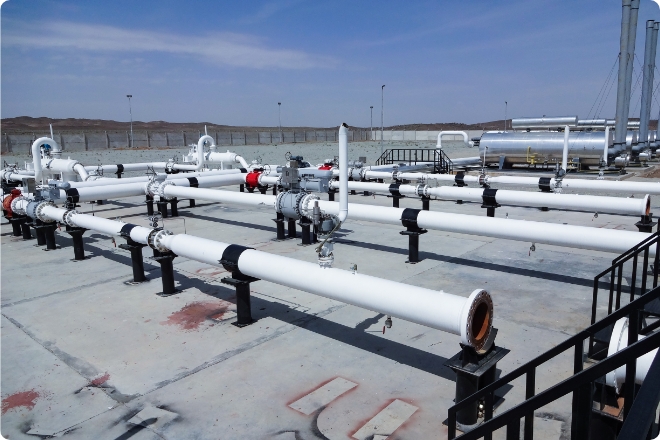
At PANS, we know what happens when high-pressure valves fail – and we’ve built our entire process around preventing that. The high pressure design and testing standards of PANS valves come from decades of real-world experience with what actually works in demanding applications.
How We Design for Real Conditions
Before we build anything, our engineers run computer simulations that basically torture-test the valve design. We analyze where stress concentrations might cause problems, figure out how to minimize pressure losses that cost you energy, and make sure the valve will handle thermal cycling without developing leaks over time.
Testing That Goes Beyond the Minimum
Here’s the thing about industry standards – they’re minimums, not targets. We test every valve at 1.5 times its working pressure because we want to know it won’t fail when you get an unexpected pressure surge.
Our fire testing goes beyond what’s required because offshore platforms can’t afford valve failures during emergencies. Every piece of material gets verified and tracked so if there’s ever a question, we can trace it back to the source.
Get the Right Valve the First Time
Choosing the wrong valve for high-pressure applications costs more than money. When valves fail under extreme conditions, you face safety risks, environmental damage, and expensive plant shutdowns that could have been avoided.
We’ve been building valves for these demanding situations for over 36 years. Our team understands what works in real plants, on offshore platforms, and in chemical processing facilities where reliability matters most.
Ready to discuss your specific application? Our quality control commitment shows how we ensure every valve meets your requirements. Contact us to select the right valve configuration for your operating conditions.
Search
Categories
Tags
Product
- Ball Valve
- Floating Ball Valve
- Fully Welded Ball Valve
- Trunnion Ball Valve
- Check Valve
- Cast Lift Check Valve
- Cast Swing Check Valve
- Wafer Type Check Valve
- DIN Valve
- DIN Bellow Sealed Globe Valve
- DIN Globe Valve
- DIN Rising Stem Gate Valve
- DIN Swing Check Valve
- Forge Valve
- Forged Check Valve
- Forged Floating Ball Valve
- Forged Gate Valve
- Forged Globe Valve
- Gate Valve
- Bellow Sealed Gate Valve
- Flat Gate Valve
- Wedge Gate Valve
- Globe Valve
- Cast Globe Valve
- Plug Valve
- Eccentricity Plug Valve
- Inverted Pressure Balance Lubricated Plug Valve
- Orbit Plug Valve
- Sleeve Type Plug Valve
- Slurry Valve
- Slurry Valve
- Strainer