Benefits of Using Fully Welded Ball Valves in LNG Applications
Some of the benefits of using fully welded ball valves in LNG applications include leak-free operation, superior cryogenic performance, and extended service life. These specialized lng valves are designed to handle the extreme conditions of liquefied natural gas systems, where temperatures reach -162°C (-260°F) and reliability is critical for safe operations.
What is a Fully Welded Ball Valve
A fully welded ball valve features a valve body that is completely welded and forged as a single unit, eliminating traditional threaded connections and flanged joints. This construction creates permanent metallurgical bonds that maintain structural integrity throughout the extreme thermal cycling typical in LNG operations.
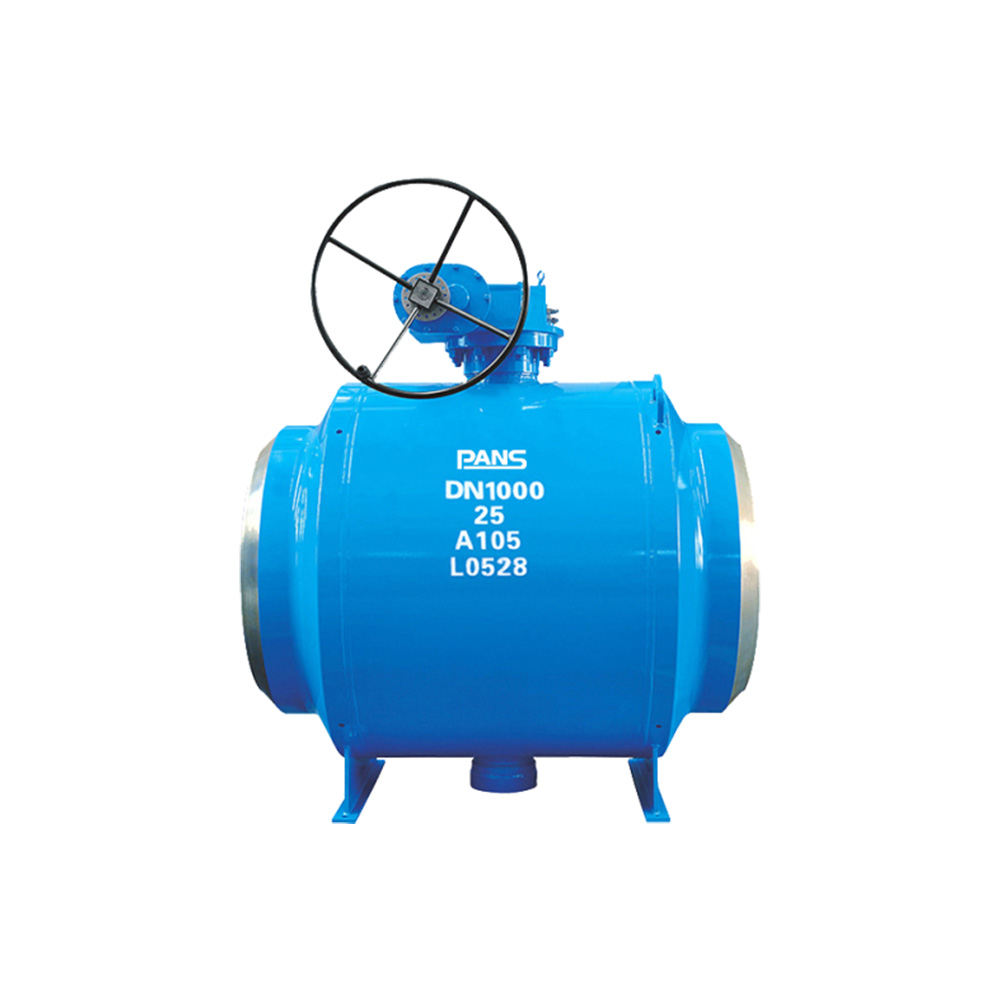
Fully Welded Ball Valve | PANS
More DetailsWhat a Solvent Weld Ball Valve
Understanding what a solvent weld ball valve offers helps clarify why it’s unsuitable for LNG applications. Solvent welded connections use chemical bonding to join components, which works adequately for standard pressure applications. However, LNG’s extreme cryogenic temperatures and high pressures quickly break down these chemical bonds, leading to joint failure and dangerous leaks.
Why LNG Applications Demand Superior Valve Technology
LNG systems create extreme operating conditions that quickly destroy conventional valve designs. The intense cold makes standard materials brittle and causes seals to fail, while high system pressures expose every weak point in traditional valve construction.
Fully welded ball valves address these challenges through their robust welded body design, which eliminates the multiple connection points where standard valves typically fail in LNG service.
Here’s a table showing the performance differences between standard, solvent and fully welded ball valves:
Performance Factor | Solvent Weld Ball Valve | Standard Ball Valve | Fully Welded Ball Valve |
---|---|---|---|
Leak Prevention | Poor | Moderate | Excellent |
Cryogenic Performance | Very Poor | Poor | Superior |
Maintenance Requirements | Very High | High | Low |
Service Life | 5-8 years | 10-15 years | 25-30 years |
Installation Flexibility | Limited | Limited | High |
LNG Suitability | Not Recommended | Poor | Excellent |
Seven Key Advantages of Fully Welded Ball Valves in LNG Service
1. Superior Leak-Free Performance
The fully welded body design virtually eliminates external leakage by reducing potential leak points. Unlike valves that rely on gaskets and threaded connections, ball valve welded construction creates a continuous metal barrier that maintains integrity even under extreme cryogenic conditions. This leak-free operation is critical for LNG facilities where even minor leaks can pose significant safety and economic risks.
2. Enhanced Durability in Cryogenic Conditions
LNG valves must withstand repeated thermal cycling and extreme temperature variations. Fully welded ball valves excel in these conditions due to their robust construction using materials specifically selected for cryogenic service, including high-nickel alloys and specialized stainless steels. The welded body eliminates weak points that could fail under thermal stress.
3. Reduced Maintenance Requirements
With fewer potential leak points and robust construction, fully welded ball valves require significantly less maintenance than traditional valve designs. This translates to reduced downtime, lower maintenance costs, and improved operational efficiency – crucial factors for LNG facilities operating on tight schedules and budgets.
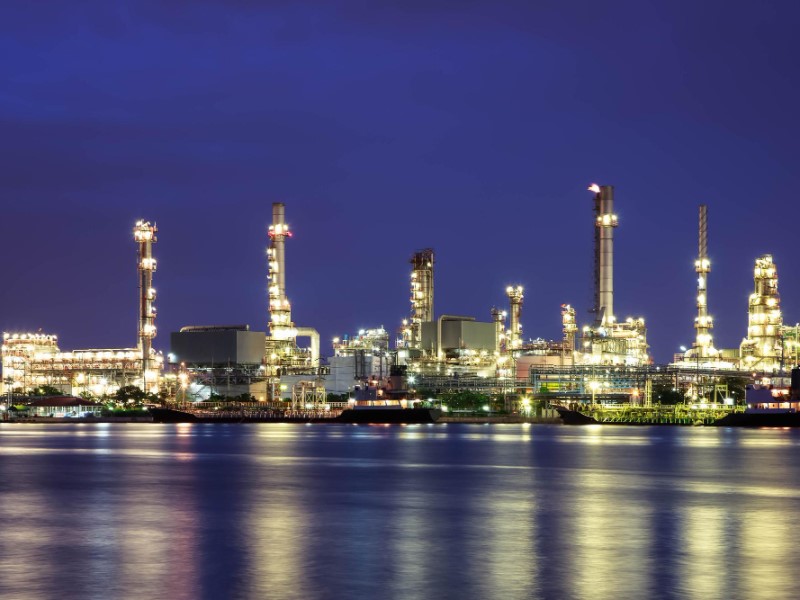
4. Direct Burial Capability
Many LNG pipeline applications require valves that can be directly buried underground. Fully welded ball valves are ideally suited for this application, eliminating the need for large valve chambers and reducing installation costs. Only a small, shallow access well is required, significantly reducing construction time and expenses.
5. Material Compatibility
Fully welded ball valves can be manufactured from the same materials used in the pipeline system, ensuring uniform thermal expansion and contraction characteristics. This compatibility prevents stress concentrations that could lead to premature failure, particularly important in LNG systems subject to seismic activity.
6. Bidirectional Sealing Performance
The ball valve design provides reliable sealing in both flow directions, essential for LNG applications where flow reversal may occur. This bidirectional capability, combined with the welded body construction, ensures consistent performance regardless of flow direction or pressure differentials.
7. Customizable Design Features
Fully welded ball valves offer flexibility in stem height and body length adjustments to meet specific installation requirements. This adaptability is particularly valuable in LNG facilities where space constraints and unique piping configurations are common.
Industry Standards and Compliance
Fully welded ball valves for LNG service must meet stringent industry standards to ensure safe, reliable operation in demanding cryogenic environments.
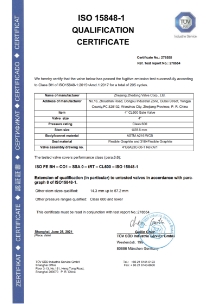
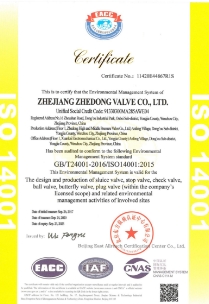
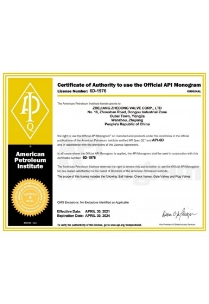
Key Standards and Requirements:
- API 6D – Pipeline valve specifications for pressure and temperature ratings
- ISO 14313 – Pipeline transportation systems for welded steel ball valves
- ASME B16.34 – Valve design standards for pressure-temperature ratings
- API 607 – Fire-safe testing to verify performance during fire exposure
- API 641 – Fugitive emissions testing for environmental compliance
- Cryogenic testing – Performance verification at actual LNG operating temperatures
These comprehensive standards and testing protocols ensure valves meet the exacting requirements of modern LNG facilities while providing long-term reliability and safety assurance.
Why PANS Valve Delivers Results
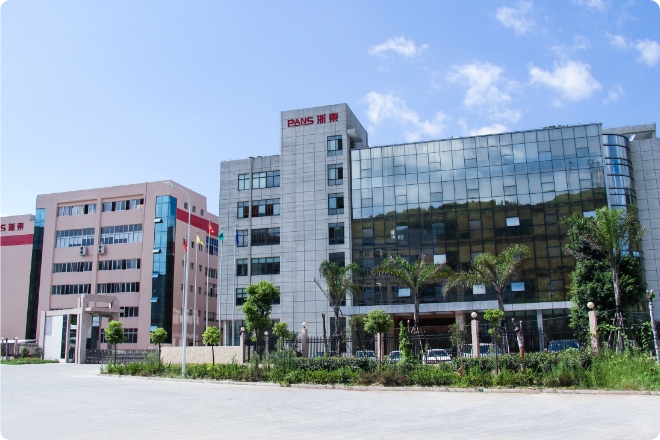
At PANS Valve, we understand the critical importance of valve reliability in LNG applications. Our fully welded ball valve designs incorporate over 36 years of manufacturing expertise, specifically engineered to meet the demanding requirements of cryogenic service.
The sealing performance and durability of PANS fully welded ball valves sets the industry standard. Our valves feature advanced sealing technologies including PCTFE seal rings with carbon content exceeding 25%, ensuring complete leak-free performance even in the most challenging LNG environments. Each valve undergoes rigorous cryogenic testing to verify performance under actual operating conditions.
What sets PANS apart:
- Computer-controlled quality that catches defects before they reach your job site
- Rigorous testing that simulates actual LNG conditions
- ISO certification and API compliance you can trust
- Sizes from 2″ to 60″ to handle any project scope
Making the Right Choice for Your LNG Project
When selecting LNG valves, consider long-term benefits: reduced maintenance costs, improved safety, extended service life, and reliable performance in harsh conditions. These advantages deliver lower total cost of ownership and enhanced project success.
PANS Valve’s comprehensive range covers sizes from 2″ to 60″ in various pressure classes, ensuring we meet your specific LNG application requirements. Our ISO-certified manufacturing and API compliance guarantee valves engineered for excellence.
Contact us today to discuss how our fully welded ball valves can enhance your LNG infrastructure project reliability and performance.
Search
Categories
Tags
Product
- Ball Valve
- Floating Ball Valve
- Fully Welded Ball Valve
- Trunnion Ball Valve
- Check Valve
- Cast Lift Check Valve
- Cast Swing Check Valve
- Wafer Type Check Valve
- DIN Valve
- DIN Bellow Sealed Globe Valve
- DIN Globe Valve
- DIN Rising Stem Gate Valve
- DIN Swing Check Valve
- Forge Valve
- Forged Check Valve
- Forged Floating Ball Valve
- Forged Gate Valve
- Forged Globe Valve
- Gate Valve
- Bellow Sealed Gate Valve
- Flat Gate Valve
- Wedge Gate Valve
- Globe Valve
- Cast Globe Valve
- Plug Valve
- Eccentricity Plug Valve
- Inverted Pressure Balance Lubricated Plug Valve
- Orbit Plug Valve
- Sleeve Type Plug Valve
- Slurry Valve
- Slurry Valve
- Strainer