Advantages of Using Forged Steel Valves in Power Plants
Some of the advantages of using forged steel valve construction in power plants include exceptional durability, superior temperature resistance, and leak-proof operation under extreme pressures. These power plant valves also have lower long-term operational costs and deliver reliable performance that maintains safety standards.
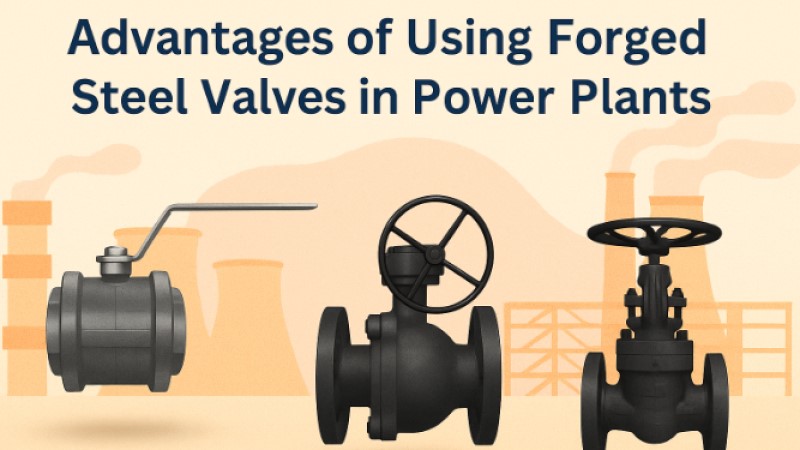
Why Power Plants Require Superior Valve Performance
Power generation facilities operate under demanding conditions that destroy conventional valve designs. Steam temperatures reach 850°F, pressures exceed 2,500 PSI, and constant thermal cycling causes standard cast valves to crack, leak, or fail completely.
Valves in power plant operations must handle superheated steam, feedwater, and process fluids reliably. When valves fail, the consequences are severe. Production stops, safety risks increase, and unplanned shutdowns can cost millions in lost revenue.
What Makes Forged Steel Valves Superior
The manufacturing process creates significant performance advantages over cast alternatives. Forged steel valves start with solid steel blocks that are heated and shaped under massive compressive forces, rather than pouring molten metal into molds.
Advanced Forging Process
Forged steel valve manufacturing creates dense, solid steel without the weak spots and internal voids common in cast valves. The forging process compresses the steel grain structure, resulting in uniform strength throughout the valve body.
This eliminates internal defects that can cause pressure-induced cracking. The result is consistent material properties that handle power plant operating conditions reliably.
Key Advantages in Power Plant Operations
Forged steel construction delivers measurable performance benefits that impact both operational costs and plant reliability:
Superior Pressure and Temperature Handling
Power plant valves must withstand pressures up to 2,500 PSI and temperatures reaching 850°F in standard applications. Forged steel construction provides the structural integrity needed for these extreme conditions without pressure-induced failure.
Temperature Performance Comparison:
Valve Type | Maximum Temperature | Pressure Rating | Typical Lifespan |
---|---|---|---|
Cast Iron | 400°F | 800 PSI | 5-8 years |
Cast Steel | 650°F | 1,500 PSI | 8-12 years |
Forged Steel | 850°F+ | 2,500+ PSI | 15-25 years |
Leak-Free Operation
Power plants require zero tolerance for valve leakage due to safety and efficiency requirements. Forged steel gate valve designs provide bubble-tight shutoff through precision-machined seating surfaces that maintain seal integrity under thermal cycling.
Reduced Maintenance Requirements
The robust forged construction significantly extends maintenance intervals compared to cast alternatives. Different types of valves used in power plant applications—gate, globe, and check valves—all benefit from the enhanced durability of forged steel construction.
This translates to longer service intervals, fewer emergency repairs, and reduced replacement costs over the valve lifecycle.
Critical Power Plant Applications
Forged steel valves are essential in the most demanding areas of power generation facilities where reliability is non-negotiable:
Steam Systems
High-pressure steam systems require valves capable of handling extreme operating conditions. Forged steel gate valve applications include main steam lines and reheat systems where temperatures exceed 850°F and pressures reach 2,500 PSI.
Turbine Operations
Steam turbines demand precise flow control and reliable isolation capabilities. Forged steel globe valves provide excellent throttling control for turbine bypass systems and extraction lines where temperature variations would compromise standard valve performance.
Feedwater Systems and Safety Applications
Boiler feedwater systems create pressure surges and thermal shock conditions that can damage conventional valves. Forged steel check valves handle these challenging conditions while preventing backflow. Emergency shutdown systems require valves that operate reliably after extended idle periods – a critical requirement that forged steel construction meets consistently.
Types of Forged Steel Valves You Need
Different jobs need different valve types, but they all benefit from forged steel construction:
Gate Valves for Isolation
Forged steel gate valve designs give you full-bore flow when open and tight shutoff when closed. Perfect for main steam isolation and turbine isolation where you need minimal pressure drop.
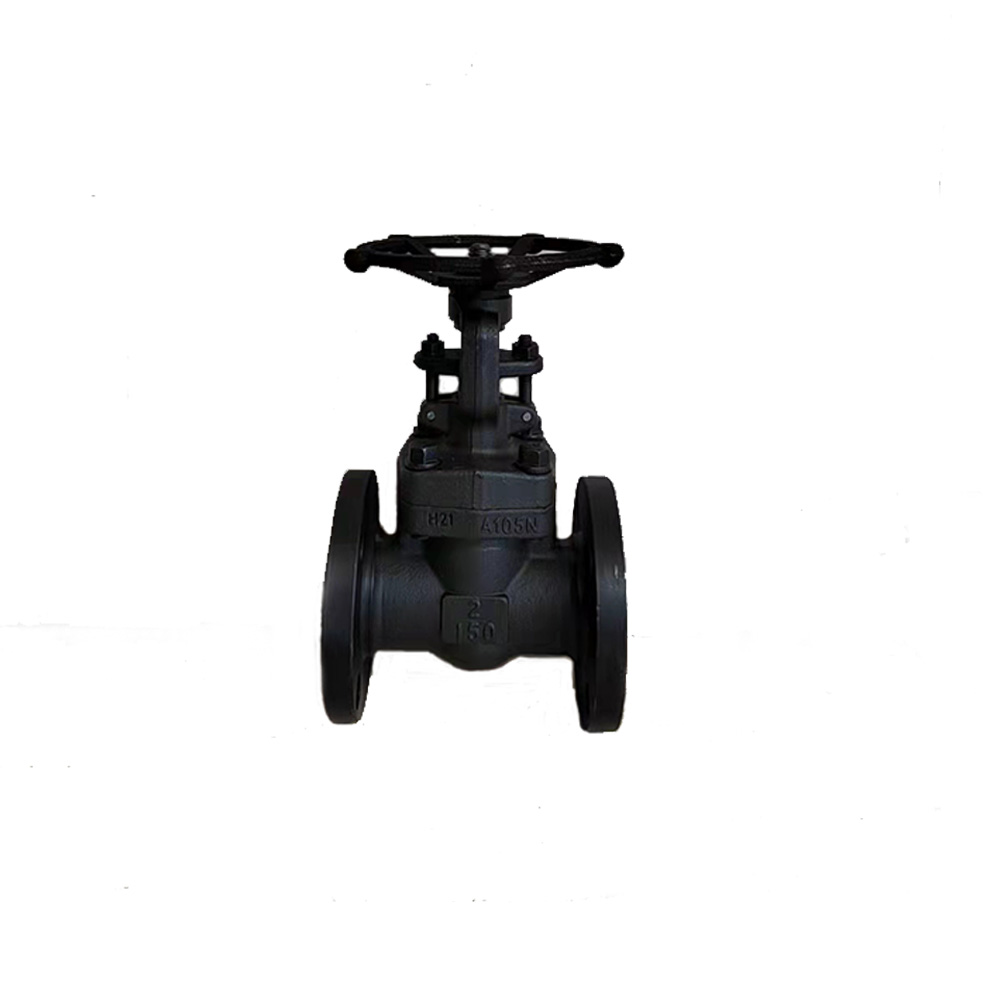
Forged Gate Valve | PANS
More DetailsGlobe Valves for Control
These excel at throttling applications where you need precise flow control. Common in turbine bypass systems and feed pump recirculation.
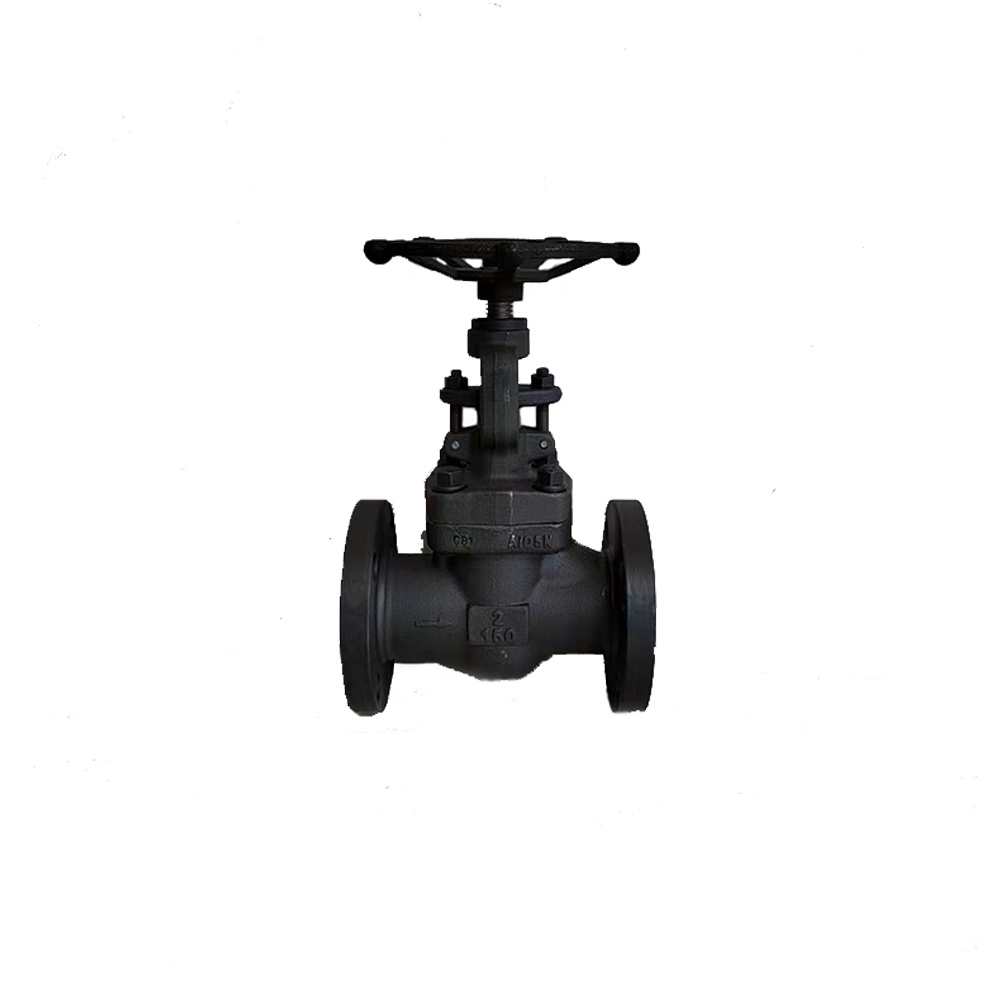
Forged Globe Valve | PANS
More DetailsCheck Valves for Protection
Prevent reverse flow in feedwater and condensate systems. Handle water hammer and pressure surges that would destroy regular valves.
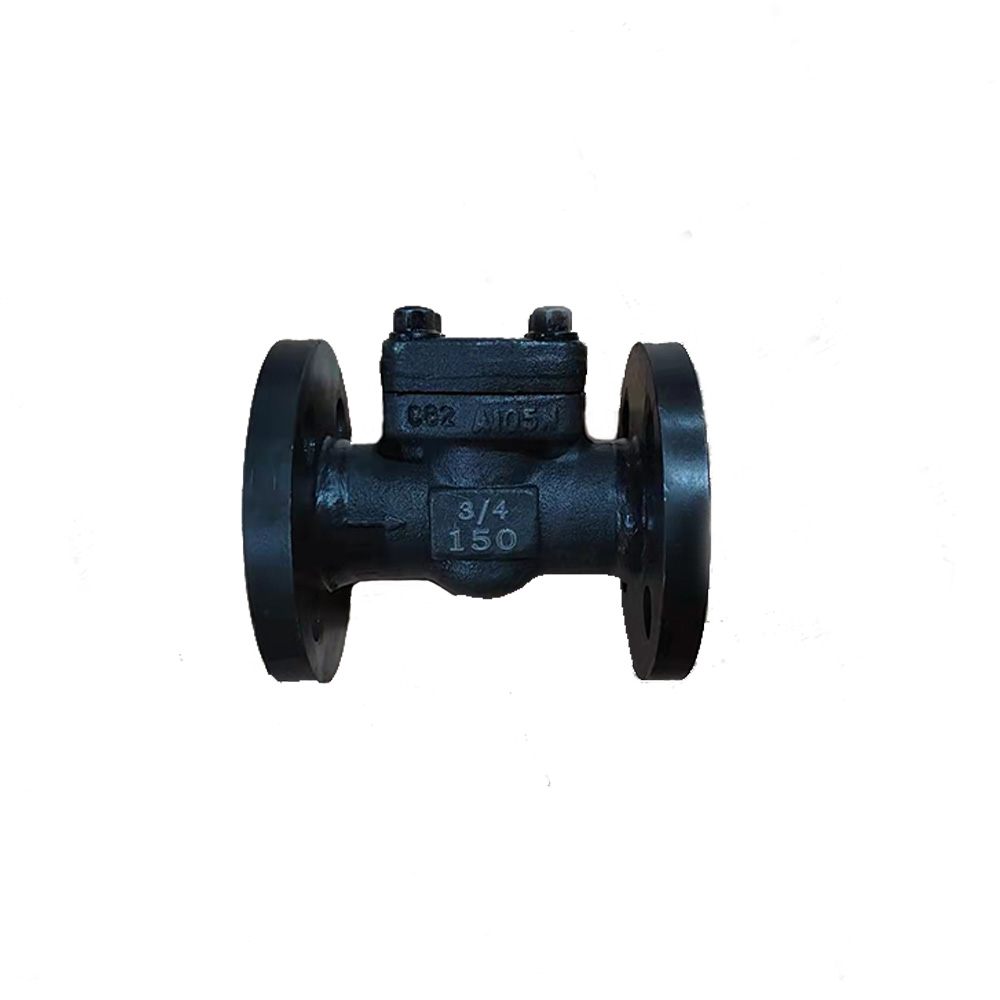
Forgede Check Valve | PANS
More DetailsEconomic Benefits for Power Plant Operations
While forged steel valves require higher initial investment than cast alternatives, they deliver superior long-term value through reduced operational costs and improved reliability:
Operational Cost Reductions:
- Fewer unplanned outages from valve failures
- Extended maintenance intervals and reduced labor costs
- Longer service life (15-25 years vs 5-8 years for cast valves)
- Improved plant availability and operational efficiency
The total cost of ownership analysis clearly favors forged steel valves when considering emergency repair costs, lost production revenue, and safety risk mitigation.
PANS Forged Steel Valve Solutions for Power Plants
The strength and reliability of PANS forged steel valves comes from over 36 years of engineering experience in demanding power generation applications. We understand the critical performance requirements that power plant operations demand.
Built for Power Plant Conditions
Our forged steel valves feature OS&Y (Outside Screw and Yoke) design with rising stem and handwheel operation, specifically engineered for high-temperature steam service. The integral seat ring construction provides reliable sealing under thermal cycling, while the choice of plug or ball configuration ensures optimal performance for different power plant applications.
Proven Quality and Compliance
PANS maintains comprehensive certifications including ISO9001 quality management, API standards compliance, CE marking, and OHSAS18001 safety standards. Our valves are manufactured to API 602 standards with ASME B16.5 flange connections and tested per API 598 protocols. They are available in pressure ratings from Class 150 through Class 2500, with SW/SC/BW/RF connection options to meet diverse power plant requirements.
Get the Right Valves for Your Power Plant
Power plant operating conditions demand forged steel construction for reliable valve performance. Standard cast valves fail under the high temperatures and pressures common in steam systems, turbine operations, and feedwater applications.
PANS Valve’s forged valve collection includes solutions built specifically for power plant conditions. Our team can help you pick the right valve configuration for your operating conditions and budget.
Contact us today to see how our forged steel valves can cut your maintenance costs and improve your plant reliability.
Search
Categories
Tags
Product
- Ball Valve
- Floating Ball Valve
- Fully Welded Ball Valve
- Trunnion Ball Valve
- Check Valve
- Cast Lift Check Valve
- Cast Swing Check Valve
- Wafer Type Check Valve
- DIN Valve
- DIN Bellow Sealed Globe Valve
- DIN Globe Valve
- DIN Rising Stem Gate Valve
- DIN Swing Check Valve
- Forge Valve
- Forged Check Valve
- Forged Floating Ball Valve
- Forged Gate Valve
- Forged Globe Valve
- Gate Valve
- Bellow Sealed Gate Valve
- Flat Gate Valve
- Wedge Gate Valve
- Globe Valve
- Cast Globe Valve
- Plug Valve
- Eccentricity Plug Valve
- Inverted Pressure Balance Lubricated Plug Valve
- Orbit Plug Valve
- Sleeve Type Plug Valve
- Slurry Valve
- Slurry Valve
- Strainer